Ryobi's die castings contribute to weight savings for automobiles. Here we introduce the features of this technology and examples of how die castings are used.
Die Casting Strengths
Die casting is a metal forming method in which metal melted at a high temperature is poured into a mold (die).
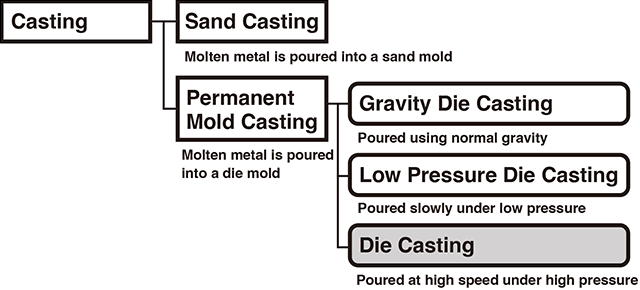
In die casting, a precision metal mold (die) is filled with molten metal at high speed under high pressure, instantly forming a product (casting). The raw materials used include non-ferrous alloys such as aluminum, magnesium and zinc.
Die casting is characterized by high dimensional accuracy and allows for the mass production of thin-walled products with complex shapes. Die casting also has the advantage of producing smooth casting surfaces requiring less machining after molding.
These advantages make die casting suited for use in making various components for automobiles, motorcycles, home appliances, office equipment, industrial machinery and builders' hardware. The Ryobi Group primarily produces parts for automobiles.
Aluminum die castings are lightweight and have excellent durability and recyclability. With the production of electric vehicles increasing in line with decarbonization targets, Ryobi is helping to improve fuel efficiency and electricity consumption by supplying lightweight, high-strength aluminum die cast products globally.
Examples of Die Casting Applications
Power train components, including cylinder blocks and transmission cases; body and chassis components, including shock towers and subframes; and components for electric vehicles. Ryobi supplies a wide variety of components to automobile manufacturers worldwide and is highly regarded for its technological capabilities and quality.
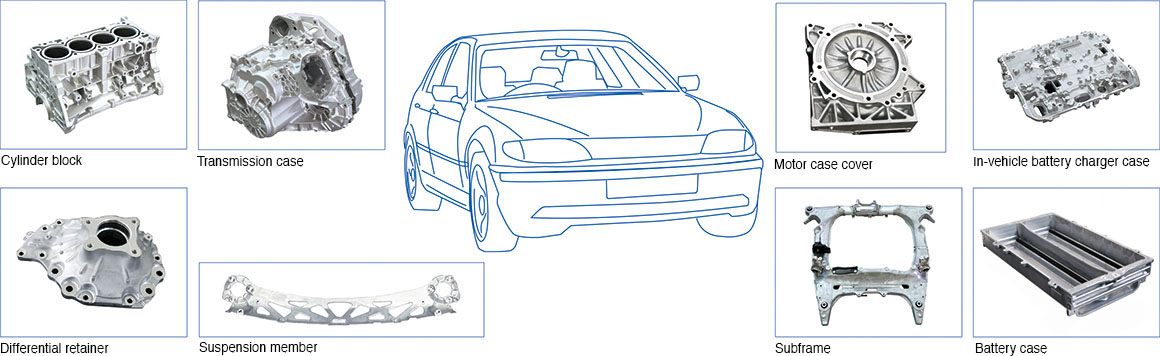